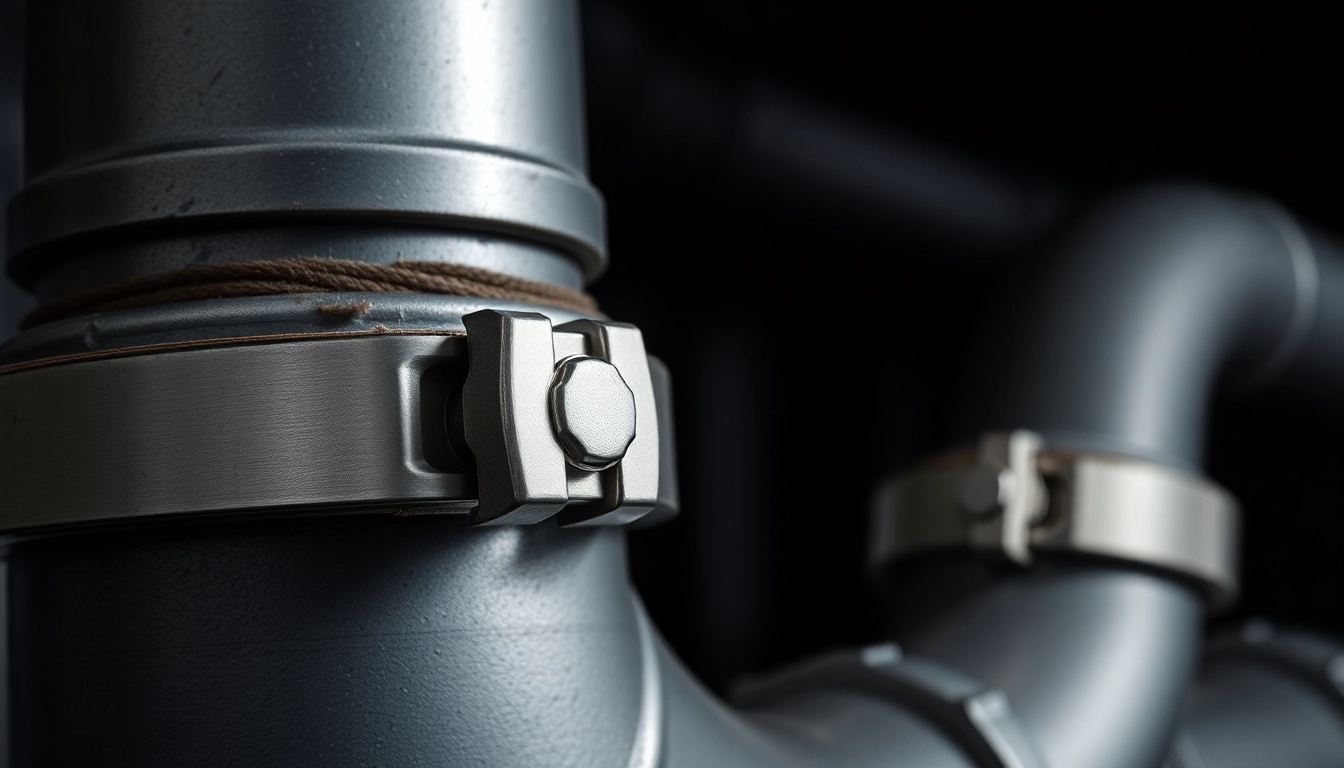
Understanding Clamp on Hose Basics
In various mechanical applications, the reliability and efficiency of connecting devices are paramount. One of the essential elements ensuring secure connections is the clamp on hose. This article delves deep into the fundamentals, applications, and choices surrounding clamp on hoses, offering a comprehensive understanding suitable for both amateurs and professionals alike.
What is a Clamp on Hose?
A clamp on hose is a flexible tube secured by a clamp mechanism designed to hold it firmly in place, preventing any leakage of fluids or gases. These hoses can be utilized across multiple applications, including automotive, industrial, plumbing, and even culinary uses. The design of a clamp on hose typically features a smooth interior surface which minimizes flow resistance, thereby optimizing performance.
Common Applications for Clamp on Hoses
Clamp on hoses find practical application across a multitude of fields:
- Automotive: Frequently utilized in engine cooling systems and fuel delivery systems, these hoses play a crucial role in vehicle operability.
- Industrial: In manufacturing, clamp on hoses are used for transferring various fluids, from water and chemicals to oils and gases.
- Plumbing: Home plumbing often employs clamp on hoses for connecting various fixtures or appliances.
- Culinary: In the food industry, they assist in piping hot or cold items—commonly found in commercial kitchens.
Types of Clamp on Hoses Available
Clamp on hoses come in several types depending on their construction materials and specific functionalities, including:
- Silicone Hoses: Known for their flexibility and resistance to heat. Ideal for high-temperature applications.
- EPDM Hoses: Excellent for outdoor applications due to their weather-resistant properties.
- Rubber Hoses: A versatile choice for a wide range of applications, providing good durability.
- Plastic Hoses: Lightweight and corrosion-resistant, typically used in lighter-duty applications.
Choosing the Right Clamp for Your Hose
Selecting the appropriate clamp for your hose is essential for ensuring its functionality and longevity. Several factors must be taken into account when making this decision.
Factors to Consider When Selecting a Clamp on Hose
Before purchasing a clamp on hose, consider the following:
- Pressure Rating: Ensure the hose and clamp can handle the intended pressure without risk of failure.
- Temperature Range: Different materials withstand different temperature ranges. Select accordingly based on your application needs.
- Environmental Conditions: If the hose will be exposed to chemicals or the outdoors, opt for materials that resist these elements.
Material Options for Durability and Performance
Hose clamps are available in various materials, each providing different benefits:
- Stainless Steel: Offers excellent corrosion resistance and strength, making it suitable for demanding environments.
- Plastic: Lightweight and resistant to corrosion but may not be suitable for high-pressure applications.
- Galvanized Steel: A budget-friendly option with decent durability but less resistance to corrosion than stainless steel.
Size Compatibility and Installation Ease
Ensure the clamp fits the hose precisely. Common sizes range from small (1/4 inch) to large (over 6 inches). It’s vital to verify the clamp’s width and the hose’s outer diameter before purchasing to ensure a secure fit. Additionally, ease of installation should be a priority—some clamps allow for tool-less adjustments, while others require specialized tools.
Installation Tips for Clamp on Hoses
Proper installation can make a significant difference in the performance and reliability of a clamp on hose. Below, we provide a step-by-step guide along with common pitfalls to avoid.
Step-by-Step Guide to Installing Your Hose Clamp
- Preparation: Ensure all parts are clean and free of debris.
- Fit the Hose: Push the hose onto the fitting until a snug fit is established.
- Position the Clamp: Slide the clamp over the hose’s end and position it at least 1/4 inch from the edge to avoid compromising the hose’s integrity.
- Tighten the Clamp: Using the appropriate tool (screwdriver, wrench, etc.), tighten the clamp securely but take care not to over-tighten, which could result in hose damage.
- Test the Connection: Activate the system to pressure check for leaks. If necessary, adjust the clamp position or tightness.
Common Mistakes to Avoid
Even seasoned professionals can make mistakes during installation:
- Improper Clamp Size: Using a clamp that’s either too small or too large can cause premature failure or leaks.
- Over-Tightening: Applying excessive force can damage the hose, leading to risk of failure.
- Ignoring Manufacturer Guidelines: Each hose and clamp type comes with specific recommendations. Neglecting these can lead to mishaps.
Tools Needed for a Successful Installation
To ensure effective installation, have the following tools handy:
- Screwdriver or wrench
- Measuring tape to check hose and clamp sizes
- Utility knife for trimming hoses if necessary
- Pressure gauge to test the connection post-installation
Maintenance and Care for Clamp on Hoses
Routine maintenance is critical for the longevity of your clamp on hoses. This section discusses how to recognize wear and tear, implement cleaning protocols, and determine when replacement is necessary.
Recognizing Wear and Tear
Over time, several signs can indicate your hose is wearing down:
- Visible Cracks: Look for abrasions or cracks, especially around the area where the clamp makes contact.
- Discoloration: Fading or discoloration of the hose material can indicate chemical degradation.
- Leaks: Any sign of moisture around the connection points should be addressed immediately.
Cleaning and Inspection Best Practices
Routine cleaning and inspections can extend the lifespan of your clamp on hoses:
- Eliminate Debris: Regularly clean the exterior of the hose to avoid buildup of dirt and grime.
- Inspect for Damage: Keep an eye out for cracks and ensure proper functionality—examine clamps as well.
- Follow Manufacturer Guidelines: Adhere to recommended cleaning intervals and procedures to ensure optimal performance.
When to Replace Your Clamp on Hose
It’s crucial to replace your clamp on hose to avoid system breakdowns. Consider the following signs that suggest it’s time for a replacement:
- Persistent leaks that cannot be resolved through tightening
- Severe discoloration or brittleness in the hose material
- Age indicators—most hoses have a lifespan that is dependent on their material and usage
Comparative Analysis of Hose Clamps
With various clamp types available, understanding the distinctions between them can aid significantly in selection. Here we compare some common options to clarify their respective advantages and ideal applications.
Comparing Worm Gear vs. T-Bolt Clamps
Worm gear clamps and T-bolt clamps are two prevalent choices, each with unique benefits:
- Worm Gear Clamps: Adjustable and widely versatile, worm gear clamps are easy to install and work well in moderate pressure environments. They are generally made of stainless steel, which offers good corrosion resistance.
- T-Bolt Clamps: T-bolt clamps provide higher clamping loads due to their design, making them suitable for high-pressure applications such as heavy machinery and industrial processes. They also ensure a uniform seal across the entire hose.
Advantages of Spring-Loaded Clamps
Spring-loaded clamps excel in applications where temperature changes might cause hose expansion or contraction. The constant tension provided by these clamps ensures that they adjust automatically to maintain an effective seal, which is critical for preventing leaks in fluctuating environments.
Real-world Applications and Case Studies
The choice of clamp can significantly affect efficiency and reliability in real-world applications. For instance, in the automotive sector, using a T-bolt clamp to secure fuel lines can prevent leaks, enhancing safety and performance. Similarly, in the food industry, employing spring-loaded clamps can ensure that piping systems adapt to varying temperatures of products being transported, upholding quality and safety standards.