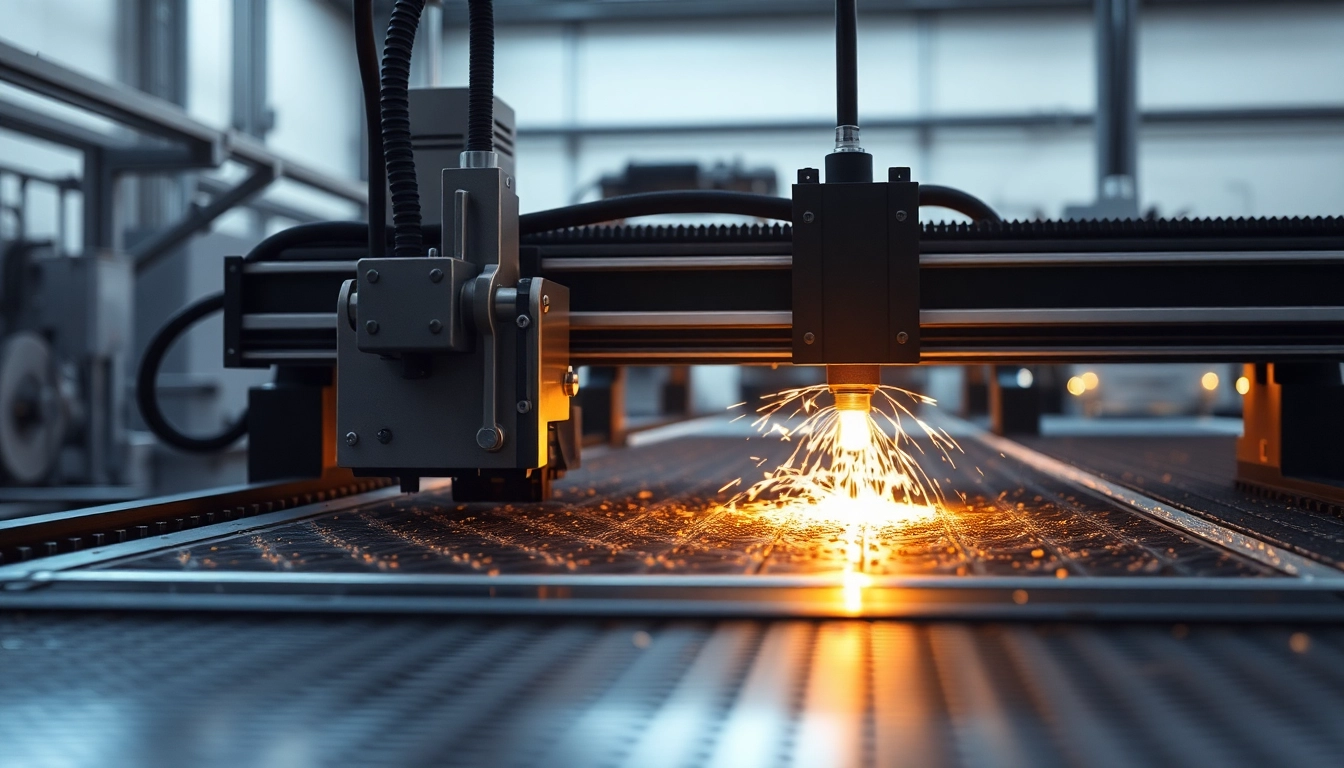
Understanding Precision Die Cutting
Precision die cutting is a specialized manufacturing process that involves using a die to cut materials into specific shapes and sizes with a high degree of accuracy. This technique is widely employed across various industries, including packaging, automotive, electronics, and medical fields. The precision achieved in this process makes it essential for applications where quality and uniformity are paramount. In this article, we will delve deeper into the intricacies of precision die cutting, its applications, materials involved, benefits over traditional methods, challenges faced, and future trends.
What is Precision Die Cutting?
At its core, precision die cutting is a method where precise dies, often made of steel or other robust materials, are used to slice through various substrates to create customized shapes. Unlike standard cutting methods, die cutting allows for intricate designs to be produced quickly and efficiently. These dies are designed specifically for the intended application, ensuring that each cut is consistent and meets precise specifications.
Applications of Precision Die Cutting
The applications of precision die cutting span a multitude of sectors, reflecting its versatility and essential nature in modern manufacturing. Some notable applications include:
- Packaging: Precision die cutting is used to create custom packaging solutions ranging from boxes and cartons to blister packs that meet the specific needs of various products.
- Automotive Parts: The automotive industry utilizes die-cut components for gaskets, seals, and insulation to ensure durability and performance under various conditions.
- Electronics: Precision-cut components are vital for electronics, where precision and reliability are critical due to the small size of many components.
- Medical Devices: In the medical field, sterile, accurate, and carefully designed components are produced through precision die cutting for devices and packaging, ensuring safety and compliance with regulatory standards.
Materials Used in Precision Die Cutting
A variety of materials can be die-cut with the precision method, depending on the final product’s requirements. Some commonly used materials include:
- Papers and Cardboards: Essential for packaging and marketing materials, these substrates can be easily shaped to fit design specifications.
- Plastics: Materials like PET, PVC, and polypropylene are often die-cut to create durable items such as cases, containers, and seals.
- Foam and Rubber: These materials provide cushioning and insulation, commonly used in automotive and medical applications.
- Metals: Thin sheets of metal can also be precision die cut for various applications, including automotive and electronics components, where strength is crucial.
Benefits of Precision Die Cutting Over Traditional Methods
Precision die cutting offers several advantages over traditional cutting methods, making it a preferred choice in many manufacturing processes.
Enhanced Accuracy and Consistency
One of the main benefits of precision die cutting is its remarkable accuracy. Unlike other cutting methods, die cutting ensures that each part produced is identical, which is crucial for quality control in mass production. This level of accuracy minimizes waste and reduces the likelihood of defective products, thus maintaining a high standard of quality.
Cost-Effectiveness for High-Volume Production
While the initial setup costs for creating a die can be significant, precision die cutting proves to be more economical in the long run for high-volume production runs. This method allows for quick production times, leading to reduced labor costs and increased output. As a result, companies can produce large quantities of items without drastically increasing costs.
Fast Turnaround Times and Customization
Precision die cutting enables rapid production and faster turnaround times compared to traditional methods. This is particularly important in industries that require quick delivery of products to meet market demands. Furthermore, the ability to easily customize designs allows manufacturers to respond effectively to changing customer needs and preferences.
Choosing the Right Precision Die Cutting Partner
Selecting the appropriate die cutting partner is imperative to ensure the best results for your project. The right choice can impact the quality of your products, production efficiency, and overall cost-effectiveness.
What to Look for in a Die Cutting Company
When evaluating potential die cutting companies, consider the following factors:
- Experience: Look for companies with a proven track record in the industry, particularly those that specialize in both your material type and required applications.
- Capabilities: Ensure the company can handle various materials and has the equipment necessary for your specific needs, including the ability to produce intricate designs.
- Quality Control: A reputable company will have strict quality control measures in place to maintain consistent output and minimize defects.
Questions to Ask Potential Vendors
To gauge a vendor’s capability and reliability, ask the following questions:
- What is your typical turnaround time for projects similar to mine?
- Can you provide samples of previous work, especially for the materials I plan to use?
- How do you ensure quality throughout the production process?
- What is your process for handling unexpected issues or challenges during production?
Evaluating Vendor Credentials and Experience
Take time to verify vendor credentials. Suppliers with industry certifications demonstrate compliance with quality standards and a commitment to excellence. Furthermore, check customer reviews and testimonials to glean insights into their reliability and service quality.
Common Challenges in Precision Die Cutting
Despite its many benefits, precision die cutting comes with its own set of challenges that companies need to navigate effectively.
Tolerances and Quality Control
Maintaining tight tolerances is a challenge in die cutting. As precision is paramount, even minor deviations can lead to significant issues in product fit and functionality. Implementing robust quality control processes is critical to mitigate this risk, such as using advanced measurement tools and conducting regular audits throughout the production process.
Material Limitations and Compatibility
Each material presents its own set of challenges. For example, some materials might not cut as cleanly as others, which can result in frayed edges or inconsistent dimensions. Understanding the specific properties of each material will help manufacturers choose the right cutting parameters and eliminate potential complications.
Adapting Designs for Die Cutting
Designs must often be adapted to meet the specifics of the die cutting process. Complex designs with intricate details may need to be simplified to ensure cutting accuracy. Collaborating with design engineers early in the process can help identify potential design flaws that could complicate production.
Future Trends in Precision Die Cutting Technology
The precision die cutting sector is evolving rapidly, driven by advancements in technology and shifting market demands. Several trends are emerging that may shape the future of this industry.
Advancements in Die Cutting Machinery
Continuous innovations in die cutting machinery are enhancing productivity and precision. Machines equipped with advanced technology, like digital or laser die cutting, provide increased flexibility and capabilities. These machines can handle a range of materials and offer rapid setup times, making them ideal for shorter production runs.
Integration of Automation and AI
The incorporation of automation and artificial intelligence into the die cutting process is on the rise. AI can analyze production data to predict maintenance needs, thus minimizing downtime. Automation streamlines material handling and speeds up the production process, allowing for a more efficient workflow.
Sustainability Practices in Die Cutting
With growing concerns over environmental impacts, many die cutting companies are adopting sustainable practices. This includes using eco-friendly materials, reducing waste through efficient cutting techniques, and investing in energy-efficient machinery. As sustainability continues to be a priority across all sectors, adopting these practices can give companies a competitive edge.