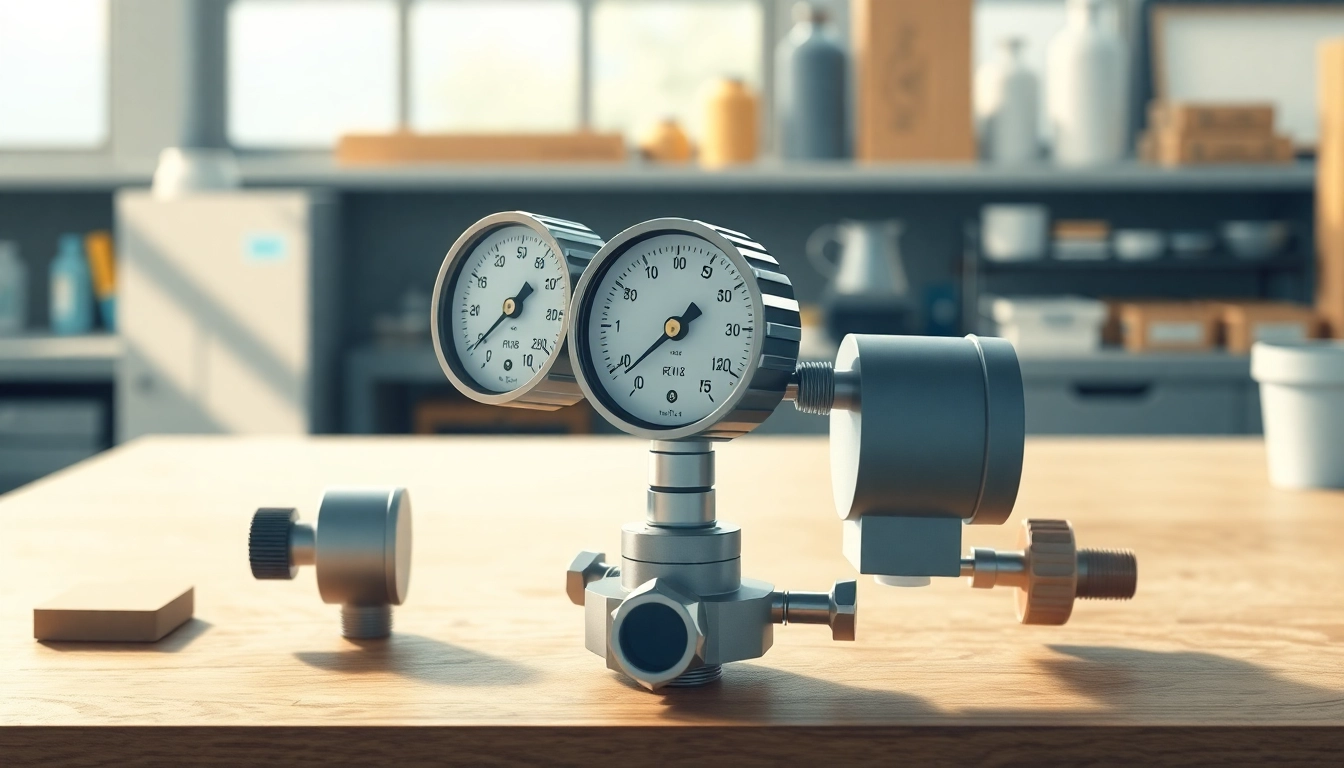
Choosing the Right Nitrogen Regulator for Your Industrial Applications
Introduction to Nitrogen Regulators
Nitrogen regulators play a vital role in numerous industries, offering precise control over gas flow and delivery pressures. Typically found in applications ranging from HVAC to food and beverage, these devices are essential for maintaining safety and efficiency. Nitrogen regulators not only serve to administer nitrogen but also vastly improve system functionality by regulating pressure and flow rates. As we delve into the intricacies of nitrogen regulators, we’ll explore their types, features, selection criteria, and offer practical tips on installation and maintenance.
What is a Nitrogen Regulator?
A nitrogen regulator is a device that controls the pressure of nitrogen gas released from a cylinder. By reducing the high pressure from the nitrogen tank to a safe and usable level, regulators enable various applications, ensuring that downstream systems operate effectively. Designed for accuracy and reliability, nitrogen regulators are specifically engineered to handle the unique properties of nitrogen, a non-reactive, colorless gas commonly used in industrial processes.
Importance of Nitrogen Regulators in Various Industries
The importance of nitrogen regulators cannot be overstated, as they play a crucial role in industries such as:
- Food and Beverage: Nitrogen is used in packaging to extend shelf life and maintain flavor integrity.
- Manufacturing: In metal fabrication and machining, nitrogen assists in protecting products from oxidation and contamination.
- Medical and Pharmaceutical: Nitrogen regulates environments in laboratories, ensuring the safe storage of sensitive materials.
Nitrogen regulators are essential in these applications as they ensure safe, reliable, and efficient operations through meticulous pressure management.
Common Applications of Nitrogen Regulators
Nitrogen regulators are utilized in various applications, including:
- Pressurization: Providing a controlled pressure environment for processes like blanketing and purging.
- Testing: Used in pressure testing to ensure sealing integrity in pipelines and vessels.
- HVAC Systems: Regulating nitrogen flow in HVAC systems for maintenance and repairs.
- Painting and Coating: Ensuring consistent pressure when spraying coatings to achieve desired finishes.
Overall, nitrogen regulators are adaptable and critical for performance across these varied applications.
Types of Nitrogen Regulators
Single Stage vs. Dual Stage Nitrogen Regulators
Nitrogen regulators come in two primary types — single stage and dual stage:
- Single Stage Regulators: These devices are designed to reduce inlet pressure to outlet pressure in one step. They are simpler and cost-effective but can be less stable if the inlet pressure varies significantly.
- Dual Stage Regulators: As the name suggests, these regulators reduce pressure in two steps, providing more stable and consistent outlet pressure, even as the cylinder pressure drops. This is particularly advantageous in applications requiring precise pressure management.
The choice between the two largely depends on the application at hand and the level of pressure stability required.
Adjustable vs. Preset Nitrogen Regulators
Another classification is based on their adjustability:
- Adjustable Regulators: These allow users to set outlet pressures according to specific needs. Ideal for versatile applications, they provide flexibility in operation.
- Preset Regulators: Factory-set to deliver a specific outlet pressure, these are straightforward and reduce the risk of user-error during adjustments. They are commonly found in applications where consistent pressure is essential.
Understanding these distinctions can help users choose the ideal regulator for their specific applications.
Choosing the Right Type for Your Needs
Selecting the right nitrogen regulator involves understanding the application requirements. Factors to consider include:
- Pressure Requirements: Determine the necessary outlet pressure based on your equipment specifications.
- Gas Flow Rate: Different gases require different flow rates, understanding your system’s requirements is critical.
- Environmental Conditions: Some settings demand more robust materials that can withstand corrosive or extreme conditions.
Thus, evaluating these parameters ensures optimal performance and longevity.
How to Select a Nitrogen Regulator
Key Features to Consider
When selecting a nitrogen regulator, it’s essential to consider several key features:
- Pressure Gauge: Integrated pressure gauges provide real-time readings to facilitate monitoring.
- Material Compatibility: Regulators should be constructed of materials suitable for nitrogen to ensure safety and longevity.
- Flow Capacity: Choose a regulator with a flow capacity appropriate for your application to avoid bottlenecks.
- Body Design: The design can affect usability and safety; look for features that provide easier handling and setup.
Identifying these features helps to ensure the selected regulator meets the demands of the specific application effectively.
Understanding Pressure Ratings
Pressure ratings are fundamental when selecting a nitrogen regulator. Key considerations include:
- Inlet Pressure Rating: Ensure the regulator can handle the maximum inlet pressure of your nitrogen cylinder.
- Outlet Pressure Rating: Verify that the outlet range supports your system’s operational requirements.
- Safety Factors: Opt for regulators that incorporate safety factors exceeding expected pressures to ensure durability.
Confidently comprehending pressure ratings is necessary for maintaining safety and efficiency in processes using nitrogen.
Compatibility with Different Systems
Compatibility with various systems is crucial. Ensure the following:
- Connection Types: Confirm that the regulator fits with the existing hookups, such as CGA580 or other industry-standard connections.
- System Components: Ensure compatibility with gauges, hoses, and other components in the nitrogen delivery system.
- Temperature and Pressure Conditions: Make sure the regulator can handle the operational conditions it will face.
Addressing compatibility upfront saves time and resources, leading to smoother operations down the line.
Installation and Maintenance Tips
Step-by-step Installation Guide
Installing a nitrogen regulator is straightforward if you follow these steps:
- Gather Materials: Ensure you have all necessary tools—wrenches, pipe tape, and safety gear.
- Prepare the Cylinder: Close the valve and check the cylinder status before beginning installation.
- Attach the Regulator: Secure the regulator to the cylinder, applying pipe tape where necessary to prevent leaks.
- Connect Hoses and Tools: Attach hoses to the regulator’s outlet and ensure all connections are tight.
- Test for Leaks: Open the cylinder slowly and check for leaks using a leak detector or soapy water solution.
- Adjust Pressure Settings: If adjustable, set the desired pressure based on your application needs.
Following these steps guarantees the regulator is installed safely and effectively.
Regular Maintenance Practices
To ensure optimal performance, establish a regular maintenance routine:
- Periodic Inspections: Regularly check for leaks, wear and tear, and signs of corrosion.
- Cleaning: Keep the regulator clean of dust and debris that may affect its effectiveness.
- Calibration: Schedule regular checks to calibrate gauges and ensure accuracy in pressure settings.
Proactive maintenance is key to preventing sudden failures and prolonging the life of your nitrogen regulator.
Troubleshooting Common Issues
Common problems with nitrogen regulators can include:
- Pressure Fluctuations: Often caused by inconsistent cylinder pressure or blockages in hoses. Resolve by ensuring adequate cylinder pressure and checking the entire system for obstructions.
- Leaking Connections: Cleaning and resealing connections can often mitigate leakage issues. Ensure that components are tightly secured and that seals are in optimal condition.
- Accurate Readings: If gauges display inaccurate readings, recalibrate or replace faulty gauges, as they can lead to incorrect pressure settings.
Identifying and rectifying these issues quickly can save you downtime and enhance the reliability of your operations.
Performance Metrics & Compliance Standards
Evaluating Efficiency of Nitrogen Regulators
When gauging the efficacy of nitrogen regulators, several performance metrics can be analyzed:
- Flow Rate: Measured in cubic feet per minute (CFM), indicating how quickly nitrogen can be delivered.
- Pressure Drop: Evaluating how much pressure is lost across the regulator allows users to identify efficiency losses.
- Adjustability Range: Features that allow for broad adjustments can enhance user flexibility in different applications.
Regularly assessing these metrics can help ensure that nitrogen regulators maintain high-level performance throughout their use.
Industry Standards and Certifications
Compliance with industry standards is crucial for ensuring the quality and safety of nitrogen regulators. Some key standards include:
- ISO 9001: A standard that ensures quality management systems are in place for manufacturing processes.
- American National Standards Institute (ANSI): Provides standards for safety, quality, and performance in manufacturing.
- Underwriters Laboratories (UL) Certification: Ensures that products meet specific safety requirements.
Choosing nitrogen regulators adhering to these standards can help avoid regulatory issues and ensure dependable and safe operation.
Comparing Performance Across Brands
When comparing different brands of nitrogen regulators, consider:
- Reputation: Established brands typically offer reliable performance backed by customer reviews.
- Warranty and Support: Brands that provide comprehensive warranties and customer support can offer additional peace of mind.
- Price Point: While cost shouldn’t be the sole factor, comparing features and performance against the price will help in making a value-based decision.
In-depth research can guide users towards brands that align with their specific application needs and budget constraints.