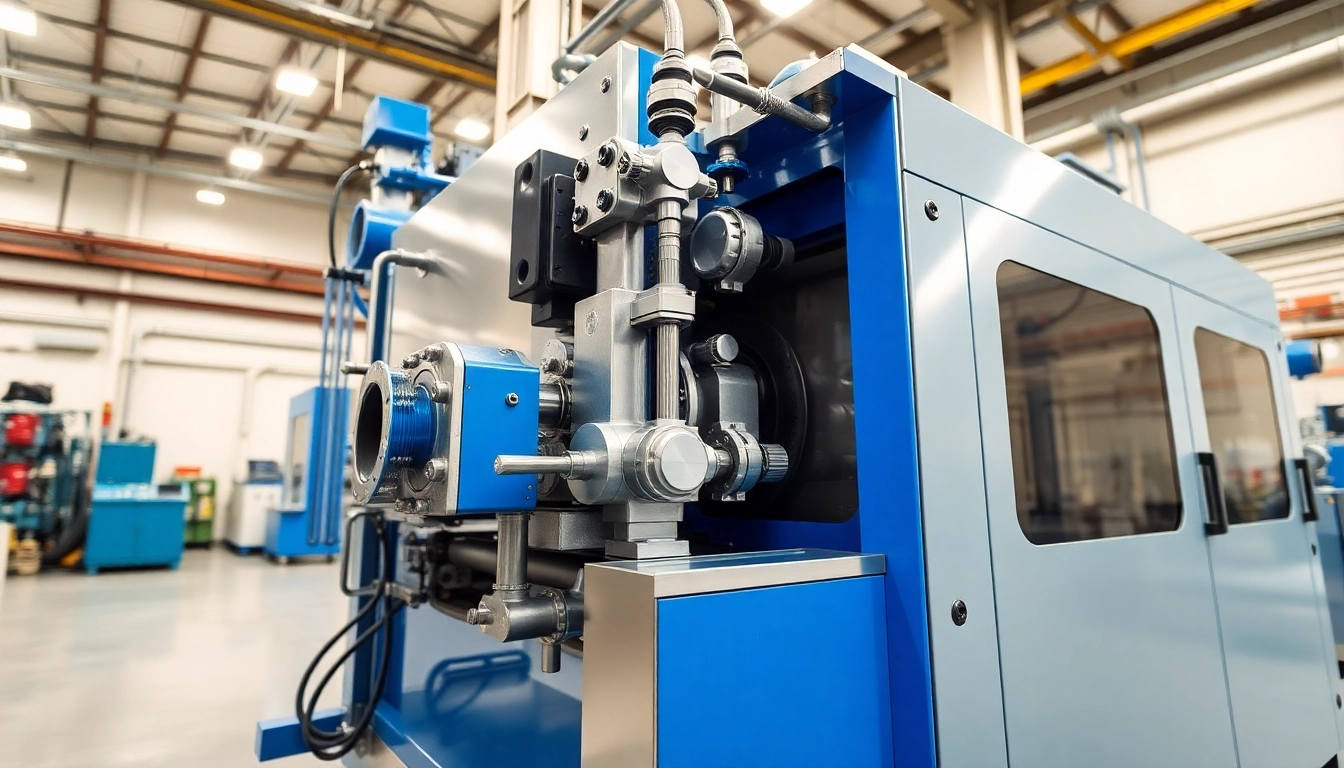
Introduction to Blow Molding Machines
In modern manufacturing, the efficiency and precision of production processes are essential for the optimal delivery of goods. One such essential machine that has revolutionized the production of hollow plastic items is the Blow Molding Machine. These machines facilitate the molding of plastic materials into complex shapes, thereby streamlining various industrial applications across multiple sectors.
What is a Blow Molding Machine?
A blow molding machine is a type of equipment used to manufacture hollow plastic products by utilizing air pressure to inflate heated plastic into a mold. The process can create items of various sizes and shapes, such as bottles, containers, and automotive components. Blow molding can be classified into several categories: extrusion blow molding (EBM), injection blow molding (IBM), and stretch blow molding (SBM). Each of these processes has its unique advantages and applications that cater to different manufacturing needs.
History and Development of Blow Molding Technology
The blow molding process has evolved significantly since its inception in the 1930s. Initially, the focus was primarily on producing glass bottles, but as plastic materials gained popularity, the blow molding industry adapted to include plastic blow molding machines. In the 1950s, advancements in thermoplastic materials and the development of more sophisticated molding technologies led to an explosion in the variety of products that could be manufactured using blow molding. Today, modern blow molding machines feature improved automation, precision engineering, and energy efficiency, making them indispensable in many manufacturing environments.
Applications of Blow Molding in Various Industries
The versatility of blow molding machines finds applications in numerous industries, such as:
- Food and Beverage: The production of bottles for soft drinks, juices, and dairy products.
- Pharmaceuticals: Creating containers and closures for medicines and health products.
- Automotive: Manufacturing components like fuel tanks, bumpers, and interior panels.
- Consumer Goods: Producing items such as toys, household containers, and personal care products.
Types of Blow Molding Processes
Extrusion Blow Molding (EBM)
Extrusion blow molding is one of the most common blow molding processes. In EBM, a thermoplastic resin is extruded into a continuous hollow tube known as a parison. The parison is then clamped between two halves of a mold, and air is blown into it to take its shape. This process is widely used for producing lightweight, high-volume items with uniform wall thickness.
Injection Blow Molding (IBM)
Injection blow molding integrates the processes of injection molding and blow molding. Initially, a preform is molded through injection; this preform is then inflated to form the final product. This method provides enhanced control over the wall thickness and is best suited for manufacturing high-precision items, such as medical containers and small consumer products.
Stretch Blow Molding (SBM)
Stretch blow molding is an advanced technique that involves stretching the preform both axially and radially while it is being blown into the final shape. This results in a stronger product with higher clarity and is particularly popular for producing lightweight PET bottles used in beverages. Stretch blow molding often follows a two-step process: the production of the preform followed by the subsequent stretching and blowing into the final shape.
Key Features and Specifications
Performance Metrics of Blow Molding Machines
The efficiency of blow molding machines can be gauged using several performance metrics, including:
- Cycle Time: The duration required to complete one production cycle, including forming, cooling, and ejection of the product.
- Production Rate: The number of units produced per hour, indicating the throughput capability of the machine.
- Material Utilization: The ratio of the actual product weight to the weight of the raw materials used, defining the efficiency of material use.
- Part-to-Part Consistency: The variability in produced items, indicating the precision of the molding process.
Energy Efficiency and Sustainability
In today’s environmentally conscious marketplace, energy efficiency is a critical consideration in selecting a blow molding machine. Modern machines are designed with energy-saving features such as optimized heating systems, efficient cooling designs, and servo-driven components that reduce energy consumption significantly. Furthermore, the use of recyclable materials in production not only minimizes waste but also aligns with global sustainability efforts.
Customization Options for Different Applications
Blow molding machines offer various customization options to cater to distinct production needs. Customizable features can include:
- Mold Design: Tailor molds to achieve specific shapes and sizes required for different products.
- Material Compatibility: Select machines compatible with various types of plastics, including high-density polyethylene (HDPE), polypropylene (PP), and others.
- Size Adjustability: Machines that can adjust their operation for different production volumes and product dimensions without extensive downtime.
Choosing the Right Blow Molding Machine
Factors to Consider When Selecting a Machine
Selecting the right blow molding machine involves understanding several critical factors:
- Production Volume: Assess your daily production needs to determine the desired output capacity of the machine.
- Type of Product: The complexity and size of the products being manufactured will influence the choice between EBM, IBM, or SBM.
- Space and Layout: Consider the space available for machinery and how it fits into your existing production line.
Cost Implications and Budgeting
Budgeting for a blow molding machine entails evaluating the initial purchase price, ongoing operational costs, and potential ROI. It’s essential to consider long-term expenditures such as maintenance, energy costs, and the costs of raw materials. Opting for a higher-quality machine may feature a larger upfront cost but could yield significant savings in efficiency and throughput over time.
Supplier Reputation and Service Agreements
The choice of supplier plays a crucial role in the reliability of the blow molding machine. A reputable vendor will offer not only robust machinery but also stellar customer service and maintenance support. It’s advisable to review customer testimonials, case studies, and inquire about service agreements, including warranty, maintenance schedules, and availability of spare parts.
Future Trends in Blow Molding Technology
Technological Innovations on the Horizon
The future of blow molding technology is poised for significant developments, with innovations targeting faster production speeds, enhanced production flexibility, and improved material properties. Technologies like AI-driven automation are expected to streamline operations, while innovations in materials science offer the potential for producing lighter, stronger products with eco-friendly characteristics.
Impact of Automation and Robotics
Automation and robotics are transforming blow molding operations, enhancing consistency and reducing labor costs. Automated systems can optimize production settings, perform quality checks during the manufacturing process, and eliminate human error, ensuring a higher quality output. As these technologies continue to evolve, they will likely play an increasingly integral role in blow molding operations.
Market Growth and Industry Insights
The blow molding market continues to expand, driven by the demand for plastic products in the packaging, automotive, and consumer goods sectors. Industry insights suggest an increasing inclination towards sustainability, with many manufacturers seeking eco-friendly materials and practices. Staying informed about market trends can help manufacturers capitalize on opportunities and address challenges effectively.