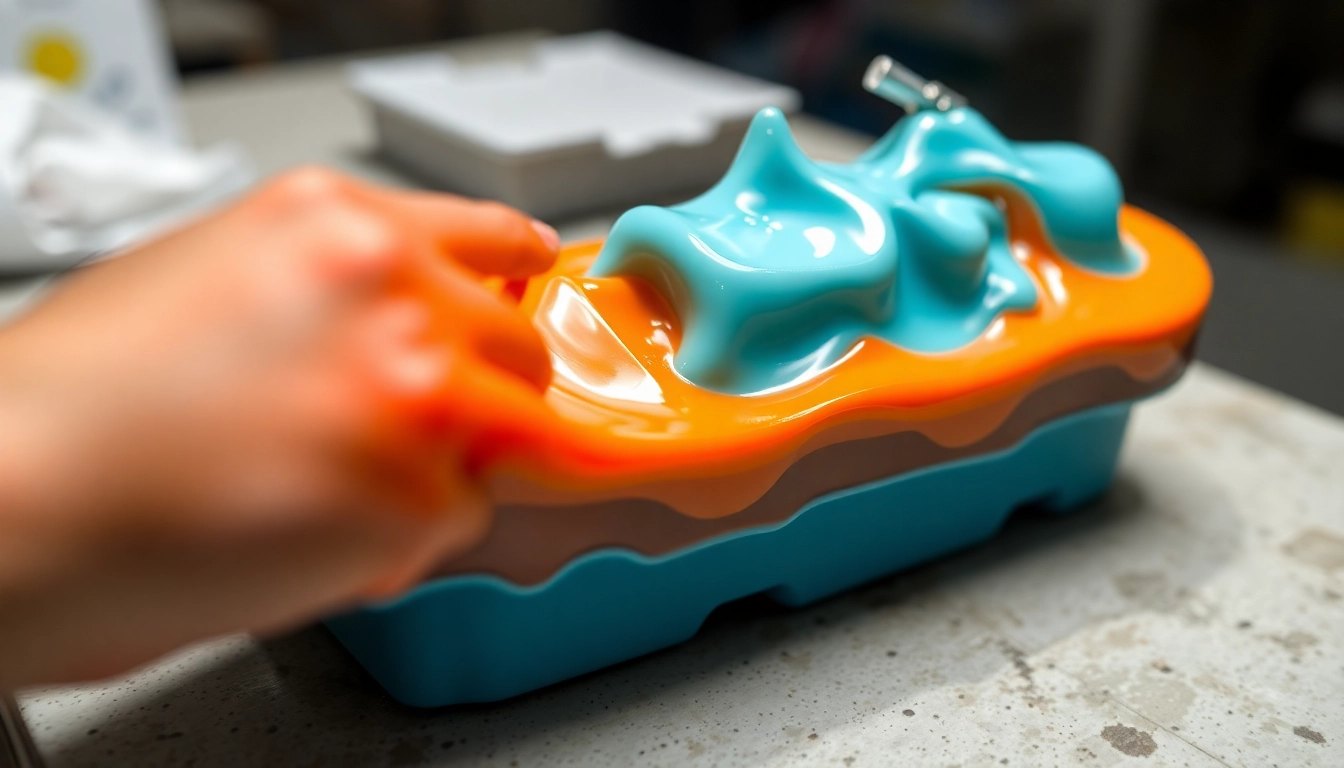
Introduction to Blow Molding Machines
Blow molding machines are an essential part of the plastic manufacturing industry, enabling the production of a wide variety of hollow plastic parts, including containers, bottles, and other products. These machines employ a sophisticated process that utilizes air pressure to create hollow shapes from molten plastic. As industries continue to seek innovative and efficient manufacturing techniques, blow molding stands out for its versatility and effectiveness. For a detailed inquiry into advanced Blow Molding Machine solutions, this article will comprehensively explore the types, benefits, and future of blow molding technology.
What is a Blow Molding Machine?
A blow molding machine is a device used to form hollow plastic objects through a process that involves heating plastic until it is soft, then inflating it inside a mold to achieve the desired shape. Typically used for production processes in the industrial sector, these machines utilize methods like extrusion, injection, or stretching of plastics, depending on the type of blow molding being performed. It is crucial to understand the basic components of a blow molding machine, which usually includes:
- Mold: A two-part fixture that shapes the plastic during the blowing process.
- Extruder: A device that melts plastic resin and shapes it into a parison.
- Blow System: Mechanism for injecting air into the parison to expand it against the mold walls.
- Clamping Unit: Holds the mold pieces together during operation.
Applications of Blow Molding Technology
The versatility of blow molding technology makes it applicable in various industries. Here are some primary applications:
- Beverage Packaging: Blow molding is widely used for producing PET bottles for soft drinks, water, and other beverages.
- Household Products: Items such as containers, cleaning bottles, and toys are also manufactured using blow molding.
- Automotive Parts: Blow molding is used to create lightweight and cost-effective parts like fuel tanks and air ducts.
- Medical Containers: Many pharmaceutical companies utilize blow molding for packaging medical supplies and equipment.
Key Benefits of Using Blow Molding Machines
Blow molding machines offer a plethora of benefits that make them ideal for producing hollow plastic products:
- Cost-Effective: High production volumes lead to lower costs per unit.
- Efficiency: Rapid cycle times allow for quick turnover in production lines.
- Material Versatility: Various types of thermoplastics can be used, providing flexibility for manufacturers.
- Customization: Molds can be tailored to meet specific design and branding requirements.
Types of Blow Molding Processes
Blow molding encompasses several processes, each suited for different applications and end products. The three primary types include:
Extrusion Blow Molding (EBM)
Extrusion Blow Molding involves the continuous extrusion of a plastic parison, which is then cut to length and molded. The process is ideal for manufacturing large containers and is characterized by:
- Simple operation, making it suitable for high-volume productions.
- The ability to produce complex shapes and sizes.
- Lower tooling and equipment costs compared to other methods.
EBM is often used for products like bottles, tanks, and jerry cans.
Injection Blow Molding (IBM)
Injection Blow Molding combines the principles of injection molding and blow molding. In this method, the plastic is first injected into a mold to form a preform, which is then blown into the final shape. IBM is frequently utilized for:
- Small production runs where high precision and tight tolerances are required.
- Creating hollow parts with complex geometries such as necks and handles.
- Medical applications that require stringent quality standards.
Injection Stretch Blow Molding (ISBM)
ISBM is a sophisticated variant of blow molding that incorporates both injection and stretching of the preform. This method enhances product strength and clarity, making it suitable for:
- Manufacturing lightweight, high-strength bottles such as those used for carbonated drinks.
- Producing bottles with better barrier properties for sensitive contents.
- Creating aesthetically pleasing designs, enhancing consumer appeal.
Choosing the Right Blow Molding Machine
Selecting the appropriate blow molding machine for your production needs is crucial for maximizing efficiency and reducing operational costs. Several key factors should be considered:
Factors to Consider in Your Selection
When choosing a blow molding machine, manufacturers should evaluate:
- Production Volume: Determine if the desired output aligns with machine capabilities.
- Type of Product: Assess if the product’s complexity can be achieved with available technology.
- Material Specifications: Evaluate which types of plastics are compatible with the machine.
- Budget: Establish a cost-effective solution that doesn’t compromise quality.
- Size of the Shop Floor: Ensure that the machine will fit within the available space.
Cost-Benefit Analysis of Different Machines
Undertaking a cost-benefit analysis can help manufacturers understand the long-term value of a blow molding machine. Key considerations include:
- Initial Purchase Cost vs. Operational Costs: Weigh the upfront investment against potential savings on materials, labor, and energy.
- Longevity and Maintenance Needs: Estimate the machine’s lifespan and the frequency of maintenance required.
- Production Efficiency: Calculate the return on investment based on production speed and output quality.
Comparative Review of Leading Brands
Integrating a brand assessment into your decision-making process can be beneficial. While there are numerous manufacturers of blow molding machines, a few notable ones include:
- Parker: Known for innovative designs that emphasize lower energy consumption and high-speed operation.
- Bekum: Offers compact machines perfect for high-quality production with quick mold changes.
- Wilmington Machinery: Specializes in high-speed rotary extrusion blow molding, particularly for multilayer applications.
Operation and Maintenance of Blow Molding Machines
The operation and upkeep of blow molding machines are vital for keeping production efficient and reducing downtime. Understanding the operational framework can lead to better management practices.
Essential Steps to Operate Your Machine
Operating a blow molding machine involves specific steps, including:
- Preparing the machine by ensuring all components are clean and lubricated.
- Setting up the mold appropriately and ensuring it is securely clamped.
- Feeding the raw material into the extruder or injector, depending on the machine type.
- Adjusting parameters such as temperature and pressure based on the material and product specifications.
- Monitoring the production cycle, ensuring quality control standards are met.
- Regularly inspecting molds and other components for wear and tear.
Routine Maintenance Best Practices
Regular maintenance is critical for extending the life of blow molding machines. Key maintenance practices include:
- Daily cleaning of the machine to remove plastic residues.
- Regular lubrication of moving parts to ensure smooth operation.
- Periodic checks on electrical components and sensors to rule out defects.
- Scheduled replacements of wear parts based on usage frequency.
Troubleshooting Common Issues
Even with proper maintenance, operators may face challenges. Key issues and solutions include:
- Inconsistent Product Quality: Review mold alignment and ensure material temperatures are optimal.
- Machine Failure: Check for electrical issues or mechanical obstructions that may interrupt operation.
- Material Wastages: Fine-tune the parison thickness and adjust the mold design for improved efficiency.
The Future of Blow Molding Technology
As technology evolves, the future of blow molding appears promising, with advancements that may redefine manufacturing processes.
Innovations and Trends to Watch
Current trends in blow molding technology include:
- Smart Manufacturing Solutions: Integration of IoT devices for real-time monitoring and analytics.
- Advanced Materials: Development of biodegradable and recycled materials for environmentally-friendly production.
- Nanotechnology: Utilizing nanomaterials to enhance product properties like strength and durability.
Sustainability in Blow Molding Production
Sustainability is becoming a major consideration among manufacturers. Innovations such as:
- Energy-efficient systems that reduce power consumption during operation.
- Recycling of plastics within the production process to minimize waste.
- Utilization of sustainable sourcing methods for raw materials.
Impact of Automation on Blow Molding Machines
Automation promises to optimize blow molding operations significantly. Key benefits of integrating automation include:
- Increased production speeds and reduced labor costs.
- Enhanced precision in processes, yielding fewer defects.
- Streamlined logistics through integrated technology providing predictive maintenance alerts.